
313 range, which is perfect for hole saw notching. Fortunately about 95% of all the work a general chassis shop does involves materials in the. After you reach material of three-eighths thickness its time to look into milling the fish-mouths.

In fact the saws perform better as material wall thickness increases. 120 or over then hole saw notching can be a very fast, accurate and easy way to cut copes. On the other hand if you do a lot of work with materials having wall thickness of. It is easier, cleaner and more accurate to cut thinner material the old fashioned way with a hand grinder. 120 wall tubing we now typically use on cycle frames is about the thinnest that can be successfully cut and still maintain accuracy.

These saws have a tendency to simply rip thinner materials. The Chopper Builders Handbook Volume II Limitations Before going much further however it should be pointed out that notching any material with a hole saw is best limited to material that has a wall or flange thickness of at least an eighth of an inch. The drawings and photos that follow depict a nice little fully adjustable notcher that is just a slight refinement on that old original concept. The saw carrier head with an inverted angle base would sit down inside one the fixture legs and slide back and forth or be clamped into position. It occurred to me that if I just welded another piece of angle to the head of a regular old joint jigger Id end up with a pretty handy little fully adjustable notching tool. That fixture, which nobody liked, was made from two pieces of one-inch angle iron with a little double acting hinge in the middle. At the time we had several dozens of fixtures in the shop for various applications and one we seldom used that I built one day in an attempt to simplify jigging parts up for tacking. The only difference was that the notcher needed to be adjustable rather than fixed in place. This might sound like a big list of features but in fact these were almost the same requirements we fulfilled on a daily basis when we built temporary welding fixtures to hold parts in position. The notcher had to be accurate to at least one-quarter degree. The notcher had to be easy to use otherwise coping with a grinder would be a better method of doing the work. The notcher had to be easy and cheap to make. For light work the notcher needed to be bench mounted in several positions.
#Chopper builders handbook full pdf portable
Notch large members or heavy structures so the notcher had to be portable and be able to clamp onto a partially finished assembly. Cut double compound notches where three members intersect and one or all three of the tubes are out of plane.
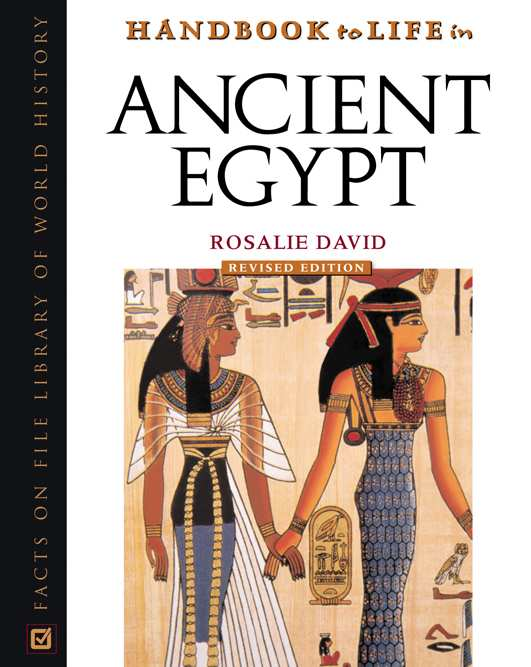
Cut compound notches where the tubes meet out of plane. Cut notches from 90 degrees to almost flat angles, as tight as just a few degrees. Cut notches in round, square or rectangular tubing as well as in angles and channel sections. What we needed was a fixture that would at least perform the following functions: 1. They say that necessity is the mother of invention and in this case the old adage was entirely true. The original Joint-Jigger and clones that were on the market just didnt do the job for the types of structures and chassis rails we were building. The Chopper Builders Handbook Volume II The Chopper Builders Handbook Notch-O-Matic Tube Notcher The Design Back in the seventies and early eighties when I was still building rods, bikes and dragsters on the side while trying to make a living doing general industrial fabrication we had a need to develop a tube notcher that used regular bi-metal hole saw bits.
